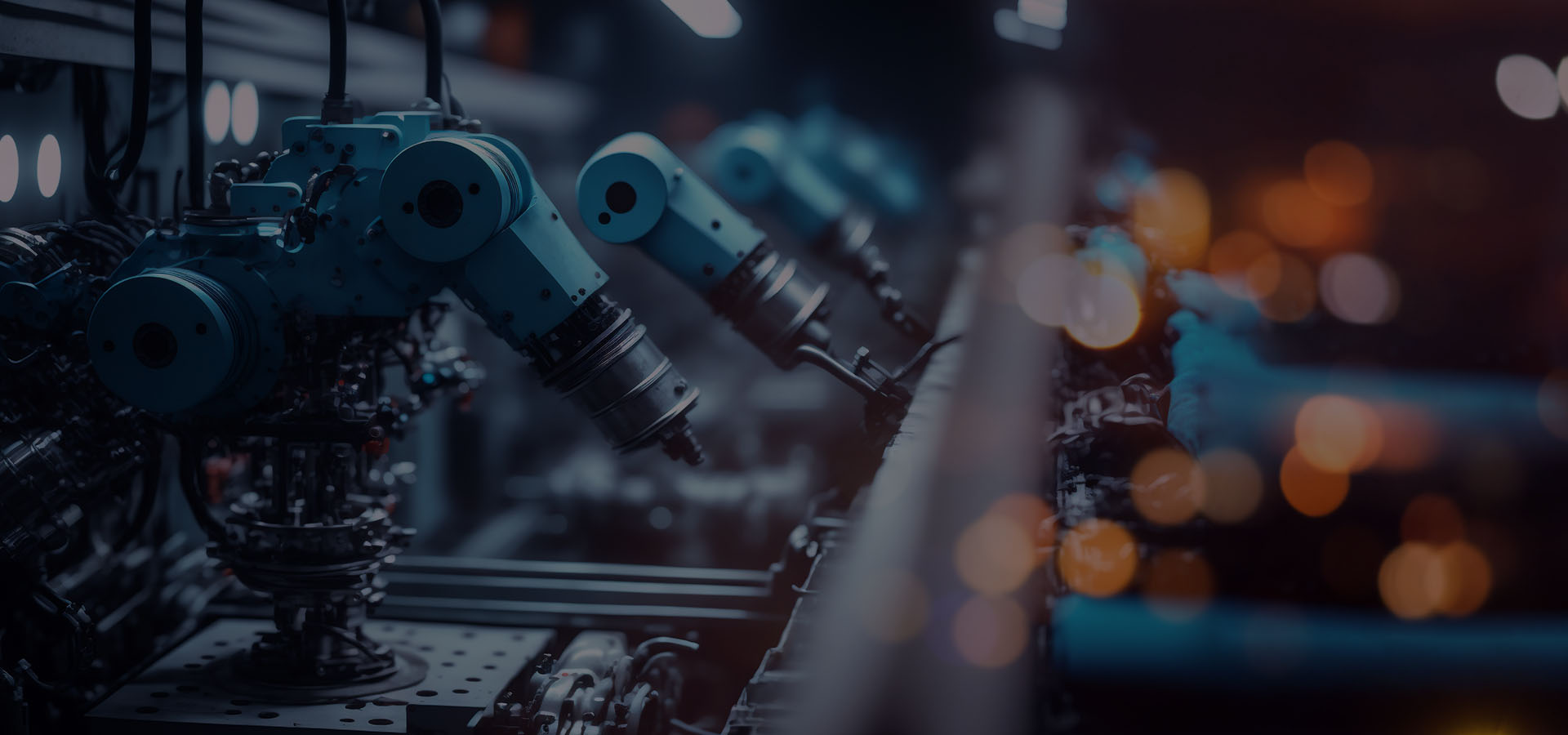
QAD Production Execution
Manufacturers need more than binders and spreadsheets to:
- Improve production efficiency for happier customers and lower manufacturing costs
- Enable high quality on the first pass, every time
- Provide management with visibility and control to prevent solvable problems from escalating
- Guarantee traceability and compliance for confidence in audits and protection against widespread recalls
Key Challenges
Focus - You invest in equipment and operators to add value to products but at some point they need to tell you about their progress. Finding the balance between making and marking is harder than it seems.
Real-time Visibility - Shipping can’t create documentation for product that isn’t reported, and maintenance can’t repair equipment if they don’t know it is down. Delays in information awareness can cause significant financial loss.
Cooperation - Production requires activity from back-office schedulers, warehouse handlers and shop floor operators. An issue in one area disrupts all, so close alignment is required to keep the right parts moving to the right place at the right time.
Data Validity - Are you sure that six isn’t the letter o? Are your material handlers confident in the inventory printout, or do they look at a picklist and walk to where they last saw those parts?
Capabilities
- Designed for the Floor
- Collaborative
- Contextual
- Seamlessly Extended
Poor collaboration between planning and operations makes it difficult for a manufacturer to meet customers’ needs. Manufacturers need timely and accurate insight into planned production. Insufficient or incorrect data interferes with production’s ability to respond effectively to unpredictable customer demands, inventory shortages, equipment failures or supply chain interruptions, or labor shortages.
Flawed data results from manual processes, out-of-date input or poor integration. For example, paper-based or manual reporting from the plant floor is inherently slow and may be of inconsistent quality. Product genealogy and traceability information may be trapped in siloed systems, preventing effective handling of recalls.
Leading manufacturers want to collect and connect operational data across all information silos. With complete and immediate access to data, it is possible to optimize production and rapidly respond to exceptions. Plus, greater operational insight leads to improved decision making, enhanced customer satisfaction and effective inventory management.
Customers expect shorter order cycles and are less tolerant of delays. A digital transformation of the manufacturing enterprise is essential to optimizing production, making sustainability progress and exceeding customer expectations.
Benefits
Enhance schedule accuracy by sharing priorities
Boost overall equipment effectiveness
Better coordinate the management of material, labor and equipment
Eliminate dependency on paper and spreadsheets
Improve operational efficiencies
Streamline planning and shop floor communication
Reduce paper, energy, and material waste to improve sustainability metrics
SOLUTION
QAD Production Execution provides the production insights needed to rapidly respond to unplanned inventory shortages, equipment failures and productivity slowdowns. It allows manufacturers to directly tie QAD Adaptive ERP and shop floor operational data and processes together to manage shop floor activities in real time. Key capabilities include:
Optimized operator-centric interface is a highly visual, contextual and intuitive interface for shop floor transactions. This results in fewer paper-based processes and improved shop floor data integrity.
Comprehensive operational data capture provides time-stamped production order, operator and equipment events, delivering the information foundation for actionable analytics and product traceability requirements
Data-driven decision making through collaboration between planning and operations maximizes cross-functional awareness of active status and immediate access to order progress. Exception management drives a shorter time to knowledge and faster, clearer insights.
Strategic information alignment provides operational extension of QAD Adaptive ERP. This extended capability results in uniform access to application data and a streamlined application. Strategic touch-points with QAD Automation Solutions and QAD EQMS (Enterprise Quality Management System) further extend the manufacturer’s connection to the complete enterprise.
System flexibility, integration and ease of maintenance allow manufacturers to adapt to a wide variety of production environments while maintaining a standardized connection to core ERP and business systems functionality. This results in an optimal response to change as well as a reduction in support costs.
Are You Ready to Cut Overtime and Improve Quality Like Noble Biomaterials?
“We have improved data quality, eliminated the overtime and now have that cost savings as a result.”
Further Information
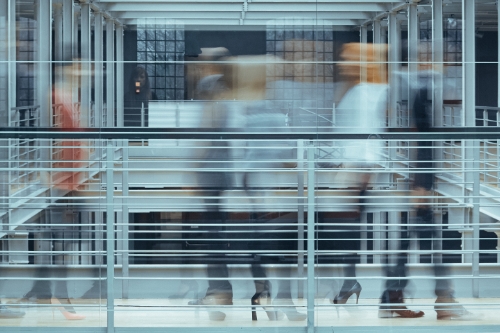
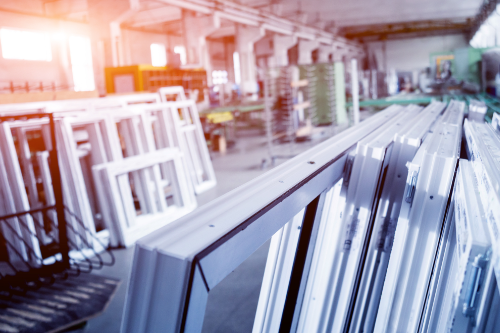
You Asked, We Answered: An MES Q&A
Vamos Conversar
Estou interessando nas Aplicações Adaptáveis da QAD.
Agradecemos por entrar em contato com a QAD! Sua solicitação foi encaminhada para o representante adequado, o qual entrará em contato logo.
Nesse meio tempo, para mais informações sobre como podemos trabalhar juntos para construir sua empresa eficaz, tire um momento para:
Inscrever-se no blog da QAD para comentários das últimas notícias e anúncios da QAD e da indústria.
Caso queira mudar suas configurações de mensagens, visite nosso centro de preferência de inscrição.