Advances in Bioinspired Superhydrophobic Surfaces Made from Silicones: Fabrication and Application
- PMID: 36771848
- PMCID: PMC9919805
- DOI: 10.3390/polym15030543
Advances in Bioinspired Superhydrophobic Surfaces Made from Silicones: Fabrication and Application
Abstract
As research on superhydrophobic materials inspired by the self-cleaning and water-repellent properties of plants and animals in nature continues, the superhydrophobic preparation methods and the applications of superhydrophobic surfaces are widely reported. Silicones are preferred for the preparation of superhydrophobic materials because of their inherent hydrophobicity and strong processing ability. In the preparation of superhydrophobic materials, silicones can both form micro-/nano-structures with dehydration condensation and reduce the surface energy of the material surface because of their intrinsic hydrophobicity. The superhydrophobic layers of silicone substrates are characterized by simple and fast reactions, high-temperature resistance, UV resistance, and anti-aging. Although silicone superhydrophobic materials have the disadvantages of relatively low mechanical stability, this can be improved by the rational design of the material structure. Herein, we summarize the superhydrophobic surfaces made from silicone substrates, including the cross-linking processes of silicones through dehydration condensation and hydrosilation, and the surface hydrophobic modification by grafting hydrophobic silicones. The applications of silicone-based superhydrophobic surfaces have been introduced such as self-cleaning, corrosion resistance, oil-water separation, etc. This review article should provide an overview to the bioinspired superhydrophobic surfaces of silicone-based materials, and serve as inspiration for the development of polymer interfaces and colloid science.
Keywords: bioinspiration; micro–nano structures; self-cleaning; silicones; superhydrophobic; water repellent.
Conflict of interest statement
The authors declare no conflict of interest.
Figures
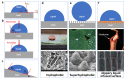
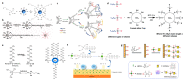
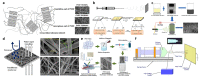
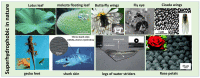
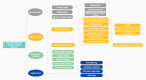
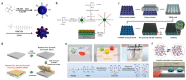
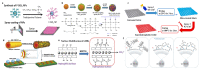
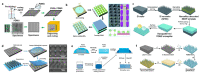
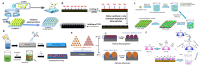
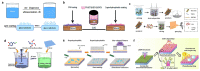
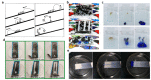
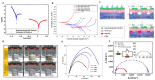
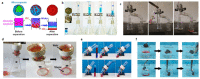
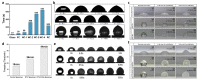
Similar articles
-
Recent Developments in the Fabrication and Application of Superhydrophobic Suraces.Chem Rec. 2024 Sep;24(9):e202400065. doi: 10.1002/tcr.202400065. Epub 2024 Sep 9. Chem Rec. 2024. PMID: 39248661 Review.
-
Development of a Superhydrophobic Protection Mechanism and Coating Materials for Cement Concrete Surfaces.Materials (Basel). 2024 Sep 5;17(17):4390. doi: 10.3390/ma17174390. Materials (Basel). 2024. PMID: 39274780 Free PMC article.
-
Hydrophobic and superhydrophobic surfaces fabricated using atmospheric pressure cold plasma technology: A review.Adv Colloid Interface Sci. 2018 Apr;254:1-21. doi: 10.1016/j.cis.2018.03.009. Epub 2018 Mar 29. Adv Colloid Interface Sci. 2018. PMID: 29636183 Review.
-
Water-Repellent Properties of Superhydrophobic and Lubricant-Infused "Slippery" Surfaces: A Brief Study on the Functions and Applications.ACS Appl Mater Interfaces. 2016 Feb 17;8(6):3615-23. doi: 10.1021/acsami.5b07881. Epub 2015 Oct 8. ACS Appl Mater Interfaces. 2016. PMID: 26447551
-
Superhydrophobic Non-Metallic Surfaces with Multiscale Nano/Micro-Structure: Fabrication and Application.Molecules. 2024 May 1;29(9):2098. doi: 10.3390/molecules29092098. Molecules. 2024. PMID: 38731589 Free PMC article. Review.
Cited by
-
The Effect of Conductive Polyaniline on the Anti-Fouling and Electromagnetic Properties of Polydimethylsiloxane Coatings.Polymers (Basel). 2023 Jul 4;15(13):2944. doi: 10.3390/polym15132944. Polymers (Basel). 2023. PMID: 37447590 Free PMC article.
-
Chemical Instability-Induced Wettability Patterns on Superhydrophobic Surfaces.Micromachines (Basel). 2024 Feb 27;15(3):329. doi: 10.3390/mi15030329. Micromachines (Basel). 2024. PMID: 38542576 Free PMC article.
References
-
- Leng X., Sun L., Long Y., Lu Y. Bioinspired superwetting materials for water manipulation. Droplet. 2022;1:139–169. doi: 10.1002/dro2.29. - DOI
-
- Barthlott W., Schimmel T., Wiersch S., Koch K., Brede M., Barczewski M., Walheim S., Weis A., Kaltenmaier A., Leder A., et al. The salvinia paradox: Superhydrophobic surfaces with hydrophilic pins for air retention under water. Adv. Mater. 2010;22:2325–2328. doi: 10.1002/adma.200904411. - DOI - PubMed
-
- Darmanin T., Guittard F. Superhydrophobic and superoleophobic properties in nature. Mater. Today. 2015;18:273–285. doi: 10.1016/j.mattod.2015.01.001. - DOI
Publication types
Grants and funding
LinkOut - more resources
Full Text Sources
Research Materials