Cellulose-Chitosan Functional Biocomposites
- PMID: 36679314
- PMCID: PMC9863338
- DOI: 10.3390/polym15020425
Cellulose-Chitosan Functional Biocomposites
Abstract
Here, we present a detailed review of recent research and achievements in the field of combining two extremely important polysaccharides; namely, cellulose and chitosan. The most important properties of the two polysaccharides are outlined, giving rise to the interest in their combination. We present various structures and forms of composite materials that have been developed recently. Thus, aerogels, hydrogels, films, foams, membranes, fibres, and nanofibres are discussed, alongside the main techniques for their fabrication, such as coextrusion, co-casting, electrospinning, coating, and adsorption. It is shown that the combination of bacterial cellulose with chitosan has recently gained increasing attention. This is particularly attractive, because both are representative of a biopolymer that is biodegradable and friendly to humans and the environment. The rising standard of living and growing environmental awareness are the driving forces for the development of these materials. In this review, we have shown that the field of combining these two extraordinary polysaccharides is an inexhaustible source of ideas and opportunities for the development of advanced functional materials.
Keywords: biocomposites; cellulose–chitosan; fibres; films; functional materials; hydrogels; nanofibers.
Conflict of interest statement
The authors declare no conflict of interest.
Figures
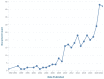
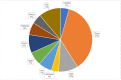

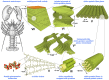
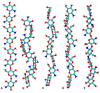
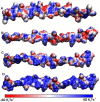
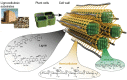
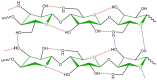
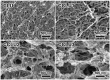
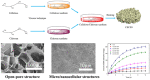
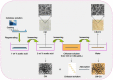
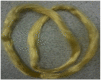
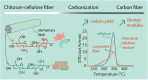
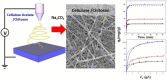
Similar articles
-
A review on chitosan-cellulose blends and nanocellulose reinforced chitosan biocomposites: Properties and their applications.Carbohydr Polym. 2016 Oct 5;150:216-26. doi: 10.1016/j.carbpol.2016.05.028. Epub 2016 May 14. Carbohydr Polym. 2016. PMID: 27312632 Review.
-
Biocomposites of copper-containing mesoporous bioactive glass and nanofibrillated cellulose: Biocompatibility and angiogenic promotion in chronic wound healing application.Acta Biomater. 2016 Dec;46:286-298. doi: 10.1016/j.actbio.2016.09.021. Epub 2016 Sep 17. Acta Biomater. 2016. PMID: 27646503
-
Nanocellulose reinforced chitosan composite films as affected by nanofiller loading and plasticizer content.J Food Sci. 2010 Jan-Feb;75(1):N1-7. doi: 10.1111/j.1750-3841.2009.01386.x. J Food Sci. 2010. PMID: 20492188
-
Development and properties of bacterial cellulose, curcumin, and chitosan composite biodegradable films for active packaging materials.Carbohydr Polym. 2021 May 15;260:117778. doi: 10.1016/j.carbpol.2021.117778. Epub 2021 Feb 10. Carbohydr Polym. 2021. PMID: 33712134
-
Polysaccharides in fabrication of membranes: A review.Carbohydr Polym. 2022 Apr 1;281:119041. doi: 10.1016/j.carbpol.2021.119041. Epub 2021 Dec 29. Carbohydr Polym. 2022. PMID: 35074105 Review.
Cited by
-
Natural Rubber Films Reinforced with Cellulose and Chitosan Prepared by Latex Aqueous Microdispersion.Polymers (Basel). 2024 Sep 20;16(18):2652. doi: 10.3390/polym16182652. Polymers (Basel). 2024. PMID: 39339118 Free PMC article.
-
Shrimp Waste Upcycling: Unveiling the Potential of Polysaccharides, Proteins, Carotenoids, and Fatty Acids with Emphasis on Extraction Techniques and Bioactive Properties.Mar Drugs. 2024 Mar 28;22(4):153. doi: 10.3390/md22040153. Mar Drugs. 2024. PMID: 38667770 Free PMC article. Review.
-
Antiviral functionalization of cellulose using tannic acid and tannin-rich extracts.Front Microbiol. 2023 Dec 6;14:1287167. doi: 10.3389/fmicb.2023.1287167. eCollection 2023. Front Microbiol. 2023. PMID: 38125579 Free PMC article.
-
Electrosprayed Core (Cellulose Acetate)-Shell (Polyvinylpyrrolidone) Nanoparticles for Smart Acetaminophen Delivery.Pharmaceutics. 2023 Sep 13;15(9):2314. doi: 10.3390/pharmaceutics15092314. Pharmaceutics. 2023. PMID: 37765283 Free PMC article.
-
Innovative biopolymers composite based thin film for wound healing applications.Sci Rep. 2024 Nov 9;14(1):27415. doi: 10.1038/s41598-024-79121-8. Sci Rep. 2024. PMID: 39521931 Free PMC article.
References
-
- Crini G. Historical review on chitin and chitosan biopolymers. Environ. Chem. Lett. 2019;17:1623–1643. doi: 10.1007/s10311-019-00901-0. - DOI
-
- Hasegawa M., Isogai A., Onabe F., Usuda M., Atalla R.H. Characterization of cellulose-chitosan blend films. J. Appl. Polym. Sci. 1992;45:1873–1879. doi: 10.1002/app.1992.070451101. - DOI
-
- Isogai A., Atalla R.H. Preparation of cellulose-chitosan polymer blends. Carbohydr. Polym. 1992;19:25–28. doi: 10.1016/0144-8617(92)90050-Z. - DOI
-
- Rogovina S.Z., Vikhoreva G.A., Akopova T.A., Erina N.A. Properties of Films Made from Cellulose-Chitosan Blends. Polym. Sci.. Ser. B. 1999;41:335–337.
Publication types
Grants and funding
LinkOut - more resources
Full Text Sources