Tailoring the Barrier Properties of PLA: A State-of-the-Art Review for Food Packaging Applications
- PMID: 35458376
- PMCID: PMC9029979
- DOI: 10.3390/polym14081626
Tailoring the Barrier Properties of PLA: A State-of-the-Art Review for Food Packaging Applications
Abstract
It is now well recognized that the production of petroleum-based packaging materials has created serious ecological problems for the environment due to their resistance to biodegradation. In this context, substantial research efforts have been made to promote the use of biodegradable films as sustainable alternatives to conventionally used packaging materials. Among several biopolymers, poly(lactide) (PLA) has found early application in the food industry thanks to its promising properties and is currently one of the most industrially produced bioplastics. However, more efforts are needed to enhance its performance and expand its applicability in this field, as packaging materials need to meet precise functional requirements such as suitable thermal, mechanical, and gas barrier properties. In particular, improving the mass transfer properties of materials to water vapor, oxygen, and/or carbon dioxide plays a very important role in maintaining food quality and safety, as the rate of typical food degradation reactions (i.e., oxidation, microbial development, and physical reactions) can be greatly reduced. Since most reviews dealing with the properties of PLA have mainly focused on strategies to improve its thermal and mechanical properties, this work aims to review relevant strategies to tailor the barrier properties of PLA-based materials, with the ultimate goal of providing a general guide for the design of PLA-based packaging materials with the desired mass transfer properties.
Keywords: PLA; barrier properties; biocomposites; clay nanoparticles; copolymers; food packaging; molecular dynamics; nanoconfinement.
Conflict of interest statement
The authors declare no conflict of interest.
Figures
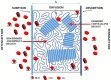
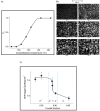
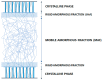
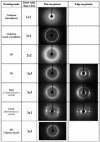
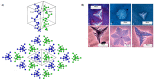
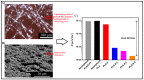
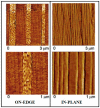
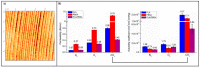
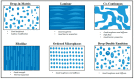
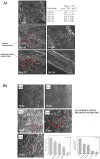
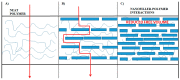
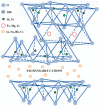
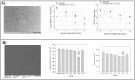
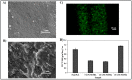
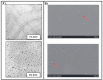
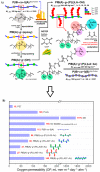
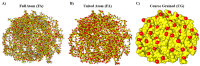
Similar articles
-
Sandwich-Architectured Poly(lactic acid)-Graphene Composite Food Packaging Films.ACS Appl Mater Interfaces. 2016 Apr 20;8(15):9994-10004. doi: 10.1021/acsami.6b02498. Epub 2016 Apr 6. ACS Appl Mater Interfaces. 2016. PMID: 27028268
-
On the Use of PLA-PHB Blends for Sustainable Food Packaging Applications.Materials (Basel). 2017 Aug 29;10(9):1008. doi: 10.3390/ma10091008. Materials (Basel). 2017. PMID: 28850102 Free PMC article. Review.
-
UV protective poly(lactic acid)/rosin films for sustainable packaging.Int J Biol Macromol. 2017 Jun;99:37-45. doi: 10.1016/j.ijbiomac.2017.01.152. Epub 2017 Feb 16. Int J Biol Macromol. 2017. PMID: 28212931
-
Bio-based active food packaging materials: Sustainable alternative to conventional petrochemical-based packaging materials.Food Res Int. 2020 Nov;137:109625. doi: 10.1016/j.foodres.2020.109625. Epub 2020 Aug 14. Food Res Int. 2020. PMID: 33233213 Review.
-
Impact of metal nanoparticles on the mechanical, barrier, optical and thermal properties of biodegradable food packaging materials.Crit Rev Food Sci Nutr. 2021;61(16):2640-2658. doi: 10.1080/10408398.2020.1783200. Epub 2020 Jul 7. Crit Rev Food Sci Nutr. 2021. PMID: 32631073 Review.
Cited by
-
Scalable Continuous Manufacturing Process of Stereocomplex PLA by Twin-Screw Extrusion.Polymers (Basel). 2023 Feb 12;15(4):922. doi: 10.3390/polym15040922. Polymers (Basel). 2023. PMID: 36850205 Free PMC article.
-
Nanocomposites with Optimized Polytetrafluoroethylene Content as a Reinforcement Agent in PA12 and PLA for Material Extrusion Additive Manufacturing.Polymers (Basel). 2023 Jun 22;15(13):2786. doi: 10.3390/polym15132786. Polymers (Basel). 2023. PMID: 37447432 Free PMC article.
-
Polylactic acid micro/nanoplastic-induced hepatotoxicity: Investigating food and air sources via multi-omics.Environ Sci Ecotechnol. 2024 May 3;21:100428. doi: 10.1016/j.ese.2024.100428. eCollection 2024 Sep. Environ Sci Ecotechnol. 2024. PMID: 38800715 Free PMC article.
-
"Polymers from Renewable Resources": Key Findings from This Topic Special Issue.Polymers (Basel). 2023 Aug 4;15(15):3300. doi: 10.3390/polym15153300. Polymers (Basel). 2023. PMID: 37571195 Free PMC article.
-
Antioxidant and Antimicrobial Effect of Biodegradable Films Containing Pitaya (Stenocereus thurberi) Extracts during the Refrigerated Storage of Fish.Antioxidants (Basel). 2023 Feb 21;12(3):544. doi: 10.3390/antiox12030544. Antioxidants (Basel). 2023. PMID: 36978792 Free PMC article.
References
-
- Leal Filho W., Saari U., Fedoruk M., Iital A., Moora H., Klöga M., Voronova V. An overview of the problems posed by plastic products and the role of extended producer responsibility in Europe. J. Clean. Prod. 2019;214:550–558. doi: 10.1016/j.jclepro.2018.12.256. - DOI
-
- Kabir E., Kaur R., Lee J., Kim K.H., Kwon E.E. Prospects of biopolymer technology as an alternative option for non-degradable plastics and sustainable management of plastic wastes. J. Clean. Prod. 2020;258:120536. doi: 10.1016/j.jclepro.2020.120536. - DOI
-
- Yadav A., Mangaraj S., Singh R., Das S.K., M N.K., Arora S. Biopolymers as packaging material in food and allied industry. Int. J. Chem. Stud. 2018;6:2411–2418.
Publication types
LinkOut - more resources
Full Text Sources