Progress of shrink polymer micro- and nanomanufacturing
- PMID: 34790360
- PMCID: PMC8566528
- DOI: 10.1038/s41378-021-00312-8
Progress of shrink polymer micro- and nanomanufacturing
Abstract
Traditional lithography plays a significant role in the fabrication of micro- and nanostructures. Nevertheless, the fabrication process still suffers from the limitations of manufacturing devices with a high aspect ratio or three-dimensional structure. Recent findings have revealed that shrink polymers attain a certain potential in micro- and nanostructure manufacturing. This technique, denoted as heat-induced shrink lithography, exhibits inherent merits, including an improved fabrication resolution by shrinking, controllable shrinkage behavior, and surface wrinkles, and an efficient fabrication process. These merits unfold new avenues, compensating for the shortcomings of traditional technologies. Manufacturing using shrink polymers is investigated in regard to its mechanism and applications. This review classifies typical applications of shrink polymers in micro- and nanostructures into the size-contraction feature and surface wrinkles. Additionally, corresponding shrinkage mechanisms and models for shrinkage, and wrinkle parameter control are examined. Regarding the size-contraction feature, this paper summarizes the progress on high-aspect-ratio devices, microchannels, self-folding structures, optical antenna arrays, and nanowires. Regarding surface wrinkles, this paper evaluates the development of wearable sensors, electrochemical sensors, energy-conversion technology, cell-alignment structures, and antibacterial surfaces. Finally, the limitations and prospects of shrink lithography are analyzed.
Keywords: Nanoscale devices; Nanoscience and technology.
© The Author(s) 2021.
Conflict of interest statement
Conflict of interestThe authors declare no competing interests.
Figures
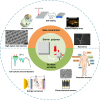
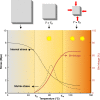
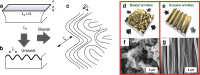
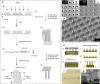
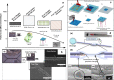
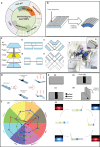
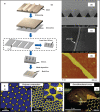
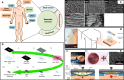
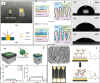
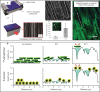
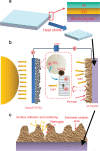
Similar articles
-
Nanoskiving: a new method to produce arrays of nanostructures.Acc Chem Res. 2008 Dec;41(12):1566-77. doi: 10.1021/ar700194y. Acc Chem Res. 2008. PMID: 18646870 Review.
-
Nanoscale Electrochemical Sensor Arrays: Redox Cycling Amplification in Dual-Electrode Systems.Acc Chem Res. 2016 Sep 20;49(9):2031-40. doi: 10.1021/acs.accounts.6b00333. Epub 2016 Sep 7. Acc Chem Res. 2016. PMID: 27602780
-
Fabrication and characterization of self-folding thermoplastic sheets using unbalanced thermal shrinkage.Soft Matter. 2017 Jun 14;13(23):4224-4230. doi: 10.1039/c6sm02637k. Soft Matter. 2017. PMID: 28504284
-
Graft-Then-Shrink: Simultaneous Generation of Antifouling Polymeric Interfaces and Localized Surface Plasmon Resonance Biosensors.ACS Appl Mater Interfaces. 2021 Nov 10;13(44):52362-52373. doi: 10.1021/acsami.1c14930. Epub 2021 Oct 27. ACS Appl Mater Interfaces. 2021. PMID: 34704743
-
Micro/Nano-Fabrication of Flexible Poly(3,4-Ethylenedioxythiophene)-Based Conductive Films for High-Performance Microdevices.Small. 2023 Jul;19(30):e2301071. doi: 10.1002/smll.202301071. Epub 2023 Apr 17. Small. 2023. PMID: 37069773 Review.
Cited by
-
Machine Learning in Predicting Printable Biomaterial Formulations for Direct Ink Writing.Research (Wash D C). 2023 Jul 18;6:0197. doi: 10.34133/research.0197. eCollection 2023. Research (Wash D C). 2023. PMID: 37469394 Free PMC article.
-
Three/Four-Dimensional Printed PLA Nano/Microstructures: Crystallization Principles and Practical Applications.Int J Mol Sci. 2023 Sep 5;24(18):13691. doi: 10.3390/ijms241813691. Int J Mol Sci. 2023. PMID: 37761994 Free PMC article. Review.
-
Strain-induced quantum Hall phenomena of excitons in graphene.Sci Rep. 2022 Feb 22;12(1):2950. doi: 10.1038/s41598-022-06486-z. Sci Rep. 2022. PMID: 35194045 Free PMC article.
References
Publication types
LinkOut - more resources
Full Text Sources