The Fabrication of Micro/Nano Structures by Laser Machining
- PMID: 31888222
- PMCID: PMC6956144
- DOI: 10.3390/nano9121789
The Fabrication of Micro/Nano Structures by Laser Machining
Abstract
Micro/nano structures have unique optical, electrical, magnetic, and thermal properties. Studies on the preparation of micro/nano structures are of considerable research value and broad development prospects. Several micro/nano structure preparation techniques have already been developed, such as photolithography, electron beam lithography, focused ion beam techniques, nanoimprint techniques. However, the available geometries directly implemented by those means are limited to the 2D mode. Laser machining, a new technology for micro/nano structural preparation, has received great attention in recent years for its wide application to almost all types of materials through a scalable, one-step method, and its unique 3D processing capabilities, high manufacturing resolution and high designability. In addition, micro/nano structures prepared by laser machining have a wide range of applications in photonics, Surface plasma resonance, optoelectronics, biochemical sensing, micro/nanofluidics, photofluidics, biomedical, and associated fields. In this paper, updated achievements of laser-assisted fabrication of micro/nano structures are reviewed and summarized. It focuses on the researchers' findings, and analyzes materials, morphology, possible applications and laser machining of micro/nano structures in detail. Seven kinds of materials are generalized, including metal, organics or polymers, semiconductors, glass, oxides, carbon materials, and piezoelectric materials. In the end, further prospects to the future of laser machining are proposed.
Keywords: application; femtosecond laser; laser machining; material; mental; micro/nano fabrication; micro/nano structures; semiconductor.
Conflict of interest statement
The authors declare no conflict of interest.
Figures
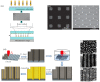
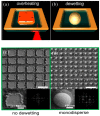
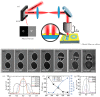
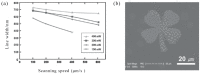
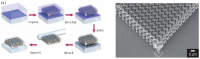
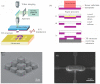
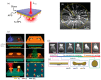
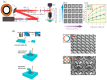
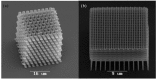
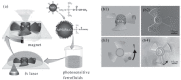
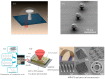
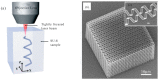
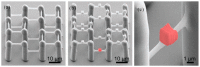
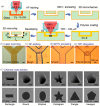
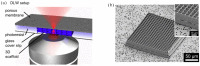
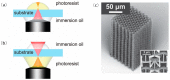

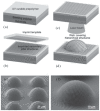
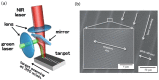
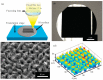
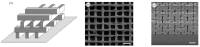
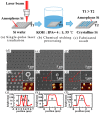
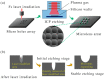
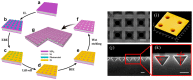
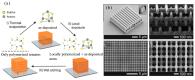
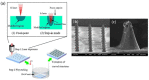
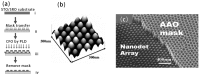
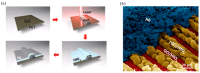
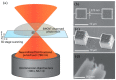
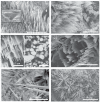
Similar articles
-
Micro/Nano Periodic Surface Structures and Performance of Stainless Steel Machined Using Femtosecond Lasers.Micromachines (Basel). 2022 Jun 20;13(6):976. doi: 10.3390/mi13060976. Micromachines (Basel). 2022. PMID: 35744590 Free PMC article. Review.
-
Optimization mechanism and applications of ultrafast laser machining towards highly designable 3D micro/nano structuring.RSC Adv. 2022 Dec 9;12(54):35227-35241. doi: 10.1039/d2ra05148f. eCollection 2022 Dec 6. RSC Adv. 2022. PMID: 36540223 Free PMC article. Review.
-
Broad-Band Ultra-Low-Reflectivity Multiscale Micro-Nano Structures by the Combination of Femtosecond Laser Ablation and In Situ Deposition.ACS Appl Mater Interfaces. 2020 Oct 28;12(43):49265-49274. doi: 10.1021/acsami.0c16894. Epub 2020 Oct 16. ACS Appl Mater Interfaces. 2020. PMID: 33064460
-
Carbon Micro/Nano Machining toward Miniaturized Device: Structural Engineering, Large-Scale Fabrication, and Performance Optimization.Small. 2024 Jul 19:e2400179. doi: 10.1002/smll.202400179. Online ahead of print. Small. 2024. PMID: 39031523 Review.
-
Advanced Micro- and Nano-Gas Sensor Technology: A Review.Sensors (Basel). 2019 Mar 14;19(6):1285. doi: 10.3390/s19061285. Sensors (Basel). 2019. PMID: 30875734 Free PMC article. Review.
Cited by
-
Three/Four-Dimensional Printed PLA Nano/Microstructures: Crystallization Principles and Practical Applications.Int J Mol Sci. 2023 Sep 5;24(18):13691. doi: 10.3390/ijms241813691. Int J Mol Sci. 2023. PMID: 37761994 Free PMC article. Review.
-
Progress of shrink polymer micro- and nanomanufacturing.Microsyst Nanoeng. 2021 Nov 3;7:88. doi: 10.1038/s41378-021-00312-8. eCollection 2021. Microsyst Nanoeng. 2021. PMID: 34790360 Free PMC article. Review.
-
Nanofabrication of Bulk Diffraction Nanogratings via Direct Ultrashort-Pulse Laser Micro-Inscription in Elastomers and Heat-Shrinkable Polymers.Nanomaterials (Basel). 2023 Apr 12;13(8):1347. doi: 10.3390/nano13081347. Nanomaterials (Basel). 2023. PMID: 37110932 Free PMC article.
-
Highly sensitive photoelectrochemical immunosensor for detecting cancer marker CA19-9 based on a new SnSe quantum dot.Mikrochim Acta. 2023 Mar 24;190(4):154. doi: 10.1007/s00604-023-05718-x. Mikrochim Acta. 2023. PMID: 36961600
-
Polystyrene Thin Films Nanostructuring by UV Femtosecond Laser Beam: From One Spot to Large Surface.Nanomaterials (Basel). 2021 Apr 21;11(5):1060. doi: 10.3390/nano11051060. Nanomaterials (Basel). 2021. PMID: 33919090 Free PMC article.
References
-
- Zang X., Zhou Q., Chang J., Liu Y., Lin L. Graphene and carbon nanotube (CNT) in MEMS/NEMS applications. Microelectron. Eng. 2015;132:192–206. doi: 10.1016/j.mee.2014.10.023. - DOI
-
- Archana P., Jose R., Vijila C., Ramakrishna S.J. Improved electron diffusion coefficient in electrospun TiO2 nanowires. J. Phys. Chem. C. 2009;113:21538–21542. doi: 10.1021/jp908238q. - DOI
-
- Bhushan B., Jung Y.C. Natural and biomimetic artificial surfaces for superhydrophobicity, self-cleaning, low adhesion, and drag reduction. Prog. Mater. Sci. 2011;56:1–108. doi: 10.1016/j.pmatsci.2010.04.003. - DOI
Publication types
Grants and funding
LinkOut - more resources
Full Text Sources