New software update drives future state of manufacturing
Sheffield, England, team implements digital innovation to meet higher production rates.
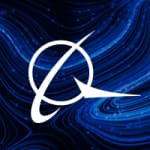
BNN
A software upgrade, developed by Boeing employees in partnership with Dassault Systems, has improved operational efficiency at the company’s Fabrication factory in Sheffield, England.
With this updated version of Apriso software, production managers’ dreams of predictability will move even closer to reality. The software capabilities were developed by the Digital Transformation team as part of its mission to modernize how the company designs and builds airplanes.
Fabrication specialists Nandipha Moyo (left) and Roisin Chapman-Allison observe production after the Apriso upgrade. In the video, employees share their experiences with the software. (Teresa Kuhn photo).
Apriso software drives factory shop order execution, displays work instructions for mechanics, manages and records all elements of the build process and provides better data for rapid decision making with a laser focus on quality. It also automates repetitive tasks and frees employees to focus on higher-value operations.
The Sheffield deployment demonstrates that the results are real, scalable and repeatable. They don’t just exist in a study or laboratory; they have a meaningful result in operations, according to Alan Wittman, director of manufacturing for Digital Transformation.
“The current implementation will enable the Sheffield site to meet higher production rates in 2023 and beyond,” Wittman said. “This initial Apriso implementation at Sheffield is our first step toward deploying our future state Manufacturing Execution System across Boeing.”
The Sheffield factory fabricates parts for the 737 MAX, but the Apriso software can be adapted to any factory setting, including Final Assembly.
Fabrication specialist Matthew Kingston prepares a new order at the Sheffield factory (Teresa Kuhn photo).
According to software product manager Dale West, “Sheffield is the first site for our digital transformation. Boeing software developers were able to customize Apriso exactly how we need it.” Dassault Systemes of France developed the off-the-shelf Apriso software product. “All the pieces are there, we just configure the features and design integrations to make it work for our Boeing production system.”
“Longer term, the ultimate benefits of all the integrated capabilities within the Apriso tool suite will deliver a 30%-plus efficiency gain across Boeing production system,” Wittman said. “These gains are achieved through reducing burden for mechanics and inspectors by delivering all needed parts, plans, tools, and information to execute production with first pass quality.”
James Needham, senior Manufacturing leader at Boeing Sheffield, said: “Since establishing Boeing’s first European manufacturing site four years ago, we have welcomed new innovations and ideas that help and drive forward our work to produce key 737 aircraft parts. This software will allow our team members to focus on utilizing their specialist skills and undertaking priority tasks, and we look forward to seeing the long-term benefits.”
“At other companies at the end of shift, you can’t tell what you’ve accomplished. Here, I can pull my card at the end of shift and see exactly what I’ve accomplished. I can see who is struggling and which machines are down,” said Joseph Kitson, Operations team lead.
Engineers (from left) Olivia Taylor, Giovandomenico Petrolo and James Holbrow observe new Apriso capabilities online. (Teresa Kuhn photo).
The upgrade has also improved the cycle time of the non-conformance reporting process, allowing the local team to evaluate the report live compared to waiting for an overseas response. “The upgrade tracks where non-conformance is occurring and in which work cell, and allows us to identify common issues. Once we understand where errors are coming from we can address them faster and more accurately,” said Bradley Hill, Quality auditor.
“I am immensely proud of our Sheffield teammates and how they exemplify the passion and talent at all of our Fabrication sites,” said Kim Pastega, Boeing Fabrication vice president and general manager. “This is just one of many examples I’ve seen of our teammates who make it possible for us to build the best commercial airplanes in the world.”
By Teresa Kuhn and Lori Gunter
Employees can send comments or feedback about this post to the BNN mailbox.