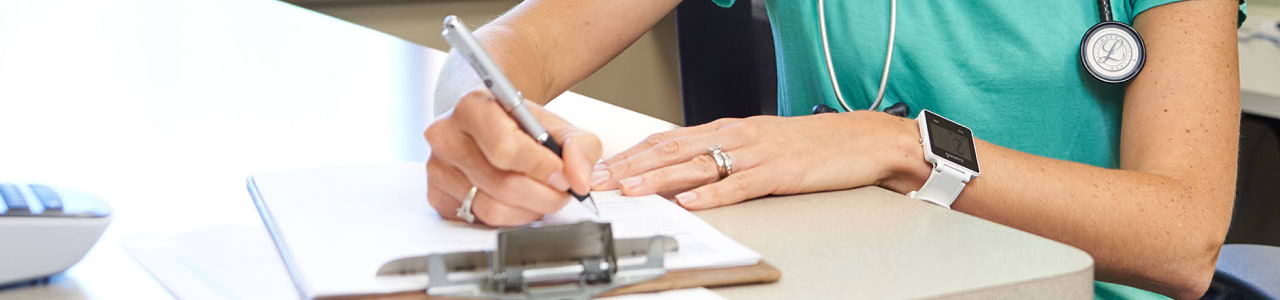
Healthcare
J. J. Keller provides the means for healthcare facilities to stay healthy themselves. In the often-shifting landscape of workplace safety in the healthcare industry, you need solutions that help you stay on top of changes. Slips, trips, and falls are common problems, and other safety topics such as hazard communication, infectious diseases, and injury and illness recordkeeping can be a challenge for even the most seasoned employees and managers. J. J. Keller provides the resources, products, and services you need to meet your unique workplace safety needs.Compliance Topics
Make sure you have the tools you need to comply with healthcare safety and compliance standards. See below for information and solutions on key safety topics.
Frequently Asked Questions
The employer must obtain and provide to the employee a copy of the evaluating healthcare professional’s written opinion within 15 days of completion of the evaluation. The healthcare professional’s written opinion for hepatitis B is limited to whether hepatitis B vaccination is indicated and if the employee received the vaccination. The written opinion for post-exposure evaluation must include information that the employee has been informed of the results of the evaluation and told about any medical conditions resulting from exposure that may require further evaluation and treatment. All other findings or diagnoses must be kept confidential and not included in the written report.
The respiratory protection standard requires an employer to retain and make available records of medical evaluations (including medical determinations and the questionnaires) in accordance with 29 CFR 1910.1020. All information from the questionnaire and/or the medical exam is confidential, and arrangements must be made by the employer to ensure it is kept confidential. Usually, the employer will have the records maintained by the PLHCP.
It will all depend upon the hazards those employees are exposed to, but in general, you should train your employees:
- Hazard communication (HazCom) and chemicals;
- Reporting incidents;
- How to use and care for all PPE required;
- Bloodborne Pathogens (assuming exposures);
- Ergonomics and proper patient lifting and moving techniques; and
- On Workplace Violence, among other topics.
Human bites are covered under the Bloodborne Pathogens Standard at 1910.1030. However, most dental offices are partially exempt from OSHA's injury and illness recordkeeping requirements. See Appendix A to Subpart B, which lists partially exempt industrial by NAICS code. NAICS code 6212 is listed for Dental Offices. If you are covered by the requirement to keep OSHA injury and illness records, then the recording of something like a human bite is regulated at 1904.8.
While there are specific requirements for marking the exits and exit routes so that “every occupant of every building or structure who is physically and mentally capable will readily know the direction of escape from any point, and each path of escape, in its entirety, shall be so arranged or marked that the way to a place of safety outside is unmistakable,” there are no requirements for posting of exit route maps. However, the posting of exit route maps is considered a “best practice.”
The standard requires that PPE be “appropriate.” PPE will be considered “appropriate” only if it does not permit blood or other potentially infectious materials (OPIM) to pass through to, or reach, the skin, employees’ underlying garments, eyes, mouth, or other mucous membranes under normal conditions of use and for the duration of time that the PPE will be used. This allows the employer to select PPE based on the type of exposure and the quantity of blood or OPIM which can be reasonably anticipated to be encountered during performance of a task or procedure.
The responsibility for providing, laundering, cleaning, repairing, replacing, and disposing of PPE at no cost to employees rests with the employer. Employers are not obligated under the standard to provide general work clothes to employees, but they are responsible for providing PPE. For example, if laboratory jackets or uniforms are intended to protect the employee’s body or clothing from contamination, they are to be provided at no cost by the employer.
The use of eye protection would be based on the reasonable anticipation of facial exposure. Masks in combination with eye protection devices, such as glasses with solid side shields, goggles, or chin-length face shields, shall be worn whenever splashes, spray, spatter, or droplets of blood or OPIM may be generated and eye, nose, or mouth contamination can be reasonably anticipated.
Sharps containers must be easily accessible to employees and located as close as feasible to the immediate area where sharps are used or can be reasonably anticipated to be found (e.g., laundries, restrooms). In areas where there may be difficulty placing sharps containers in the immediate use area, alternatives include using containers that are lockable or are designed to prevent removal of syringes while maintaining easy accessibility for discarding. If a mobile cart is used in these areas, an alternative would be to lock the sharps container onto the cart.
OSHA’s position is that EPA-registered tuberculocidal disinfectants, diluted bleach solutions, and EPA-registered disinfectants that are labeled as effective against both HIV and HBV as well as sterilants/high-level disinfectants cleared by the FDA, meet the requirement in the standard and are “appropriate” disinfectants to clean contaminated surfaces, provided that such surfaces do not become contaminated with agent(s) or volumes of or concentrations of agent(s) for which higher level disinfection is recommended. The particular disinfectant used, as well as the frequency with which it is used, will depend upon the circumstances in which a given housekeeping task occurs (i.e., location within the facility, type of surface to be cleaned, type of soil present, and tasks and procedures being performed). The employer’s written schedule for cleaning and decontamination should identify such specifics on a task-by-task basis.
There is no OSHA regulation that specifically addresses safe lifting procedures. If, during an OSHA inspector's review of an employer's records or as the result of an employee complaint, a great number of lifting injuries are uncovered which the employer has not taken steps to resolve, the employer may be cited under Section 5(a)(1) of the OSH Act, commonly referred to as the General Duty Clause. This section of the Act requires employers to provide a safe and healthful workplace for their employees.
Employers must ensure:
- Walking-working surfaces are inspected, regularly and as necessary, and maintained in a safe condition.
- Hazardous conditions on walking-working surfaces are corrected or repaired before an employee uses the walking-working surface again. If the correction or repair cannot be made immediately, the hazard must be guarded to prevent employees from using the walking-working surface until the hazard is corrected or repaired.
- When any correction or repair involves the structural integrity of the walking-working surface, a qualified person performs or supervises the correction or repair.